Abstract : A design scheme of embedded CNC system based on ARM and FPGA is proposed. The hardware and software design of the ARM system, the hardware-based fine interpolation implementation method based on FPGA and the acceleration and deceleration control strategy of the numerical control system are introduced in detail. The system combines the advantages of fast ARM operation and high computational precision with the online reconfigurability of FPGA internal logic, which improves resource utilization and real-time performance and enhances the flexibility of the CNC system. The simulation and practice results show that the whole control system has the advantages of good real-time performance, low cost and high performance.
0 Preface
In the existing numerical control system, the computer numerical control system scheme of the industrial computer plus the motion control card is adopted to design the motion controller. With the increasing complexity of the overall function of the industrial computer, the requirements for the size, cost and power consumption of the motion control system are becoming more and more demanding. The existing computer numerical control system gradually presents a disadvantage of serious waste of resources and poor real-time performance in motion control. In addition, the openness, modularization and reconfigurable design of the CNC system is a hot topic in the field of numerical control technology. The purpose is to adapt to the development of technology and to facilitate users to develop their own functions. Based on the hardware platform of ARM and FPGA, this paper designs an embedded CNC system with high openness characteristics by adopting the separation of strategy and mechanism. The numerical control system not only has the main functions of the large-scale numerical control system in the past, but also has better operability and cutting performance, and has more outstanding advantages in terms of openness, making the numerical control system application software portable and interchangeable.
1 Based on ARM and FPGA, the overall scheme of embedded CNC system
The structure of the embedded CNC system based on ARM and FPGA is shown in Figure 1. According to the idea of ​​module division, this paper divides the controller into three parts: human-computer interaction, interpolation algorithm and communication. ARM in the system uses Samsung's 16/32-bit RISC microprocessor S3C2440A, which uses the ARM920T core with a core frequency of up to 400MHz. The FPGA uses the XC3S250E from Xilinx's Spartan 3E series.
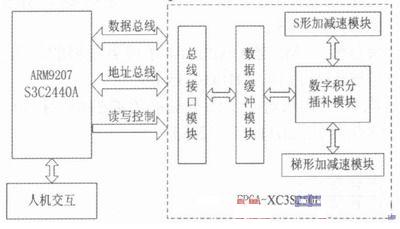
Figure 1 Embedded CNC system structure based on ARM+FPGA
2 S3C2440A control system
As the control core of the numerical control system, ARM is mainly responsible for decoding, calculating and logic processing the part processing code and control information obtained from the data memory or directly obtained from the upper PC or network, completing the coarse interpolation of the processing data and the man-machine. Interface and data communication. ARM system is the control core of the whole CNC system. Under the management of embedded operating system, the information processing and coarse interpolation operation of the whole system are realized by means of time-sharing processing, and various control commands are input through input devices such as keyboard and touch screen. The real-time running status of the numerical control system is displayed through LCD, indicator light, etc., to achieve human-machine friendly interaction. Based on S3C2440A controller, there are various communication interfaces, including RS232, RS485, Ethernet port, USB and other interface modules. File transfer and network control are implemented through these interfaces.
The overall structure of the embedded CNC software system is shown in Figure 2. The software structure of the system is mainly divided into two parts: operating system software and numerical control application software. Since the numerical control system is a real-time multi-tasking system, the real-time requirements are very high. To ensure the coordinated execution of each task, the system uses the μC/OS-II real-time operating system as a software platform.
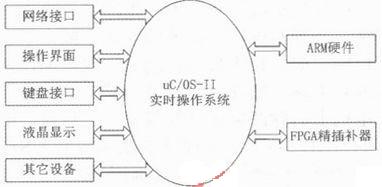
Figure 2 Overall composition of the embedded CNC software system
In order to realize the normal operation of the operating system on the S3C2440A microprocessor platform, it is necessary to modify the code related to the processor type. The work required for the operating system migration is to rewrite three files, that is, rewrite the file 0S_CPU. H, 0S_CPU_A. ASM and OS_CPU_C. C. Where 0S_CPU. H includes the processor-related variables, macros, and types defined with the #define statement. 0S_CPU_A. Several assembly language functions are defined in ASM, including the interrupt vector address of the interrupt service routine. If some C compilers allow assembly language statements to be inserted directly into C, they are not necessarily required, and the user can put the required assembly language code directly into OS_CPU_C. In the C file.
Barbecue machine is a barbecue food machinery and equipment, its main function is to do all kinds of barbecue products. Mainly used for barbecue shops, mobile barbecue and so on.
The use of rotary grill grill grilled after a piece of barbecue from the barbecue, accompanied by salad dishes, ingredients into a special made in the bread. Visibility, on-site production, and popular in Europe and the United States. Become one of the mainstream street food fast food.
1 power: the range of 800-1600W, according to the actual situation. 2 grilled food: steak, shrimp, vegetables, ham and so on. 3 functions: 3.1 baking pan with a raised stripes, relying on the protruding stripes to bake the food, there will be drainage structure, slope or drain hole. 3.2 baking time is about 3-5 minutes. 3.3 thermostat is adjustable, according to the different food or personal taste to adjust the different. 3.4 heat pipe: According to the different grades of products, choose different specifications of the heating pipe. Generally fixed in the back of the heating plate, using high temperature stainless steel tube or nickel-chromium alloy tube INCO840, the latter cost higher. 3.5 generally do not need PCB control, FireWire to increase the temperature insurance. 3.6 within the wiring: the general use of hidden lines, hidden in the activities of the hinge of the shaft. 3.7 Other: need to take oil device, a separate configuration or drawer type oil box. 3.8 turn on the power, the red power light, the machine warm, until the green light into the food, wait 3 to 5 minutes.
Electric BBQ Grill
Electric BBQ Grill,Smokeless BBQ Grill,Electric Chicken Grill,Vertical Electric BBQ Grill
Ningbo APG Machine(appliance)Co.,Ltd , http://www.apgelectrical.com